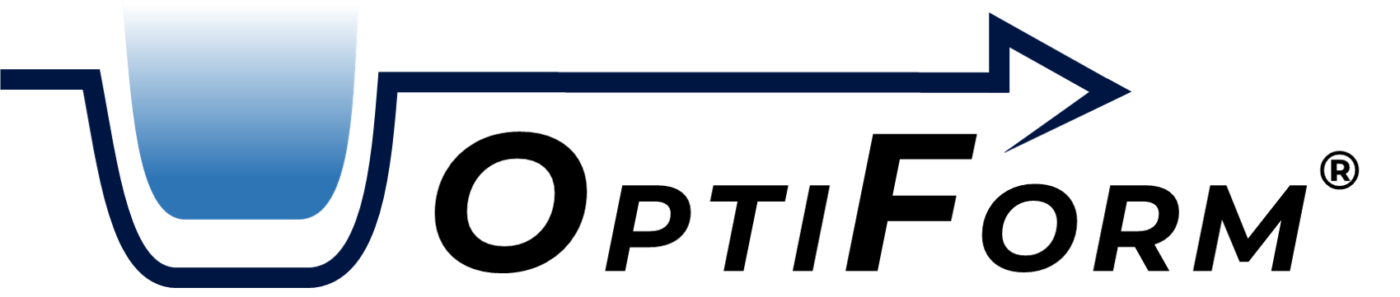
OPTIMUM PLUG ASSIST MATERIAL FOR THERMOFORMING
CGP Europe designs and manufactures high quality, innovative tooling materials used in the thermoforming industry.
CGP Europe designs and manufactures high quality, innovative tooling materials used in the thermoforming industry.
OptiForm® is a plug assist family of materials developed by CGP Europe wich combines the toughness of engineering thermoplastics with the low thermal conductivity of a syntactic foam. OptiForm® resists chips, dings and breakage that result from even the most abusive production conditions. Our materials performance are far ahead from the old generations of epoxy-based syntactic materials.
OptiForm® highly improves thickness distribution, clarity and reduces mark-off, sticking of difficult to process polymers. In addition, our materials are DUST-FREE and RECYCLABLE!
The range of product that does not make dust during machining and finishing of plugs !
OptiForm® may be used on a wide variety of sheet-fed, rotary or in-line machines. It is widely used with all types of thermoforming film: PP, PET, PLA, HIPS, PVC, PS, PE, multilayers…
With PP & PET we will give better productivity than any other epoxy syntactic.
With high toughness, machine downtime due to damaged plugs is reduced. Less downtime, lower costs, more consistent quality.
No dust collection equipment or respirators are required due to the large, non-abrasive chips. Plugs can be machined over three times faster than syntactic foam due to the easy chip formation.
OPTIFORM® is specially formulated for service up to 180°C with minimal loss in mechanical properties.
The material is provided in standard sized rods or sheets, but may be custom molded to meet your specific needs.
Plug assist is used to pre-stretch the heated plastic sheet inside the mold cavity before turning on vacuum during the thermoforming process. The pre-stretching aims at improving the thickness distribution and lots of other parameters (cycle time, mark-off, part clarity, starting gauge…).
Plugs have a geometry usually from 10 to 30% smaller than the mold cavity. They have to be made with low thermal conductivity materials such as syntactic foam otherwise they have to be heated.
The four most important parameters to take into account to get the best results with plug assist is: