Optiform VS Competitors
Optiform has already proven its skills.
As our materials are made with nylon and not epoxy like our competitors, we are able to offerproducts that are superiors in several areas!
Here your can see on the table that our products have more to give you than our competitors’.
|
|||||||||||||||||||||||||||||||||||||||||||||||||||||||||||||||||||||||||||
W – WF – S350 Formlite | FLX | FLXT – WFT | B1X – XTL |
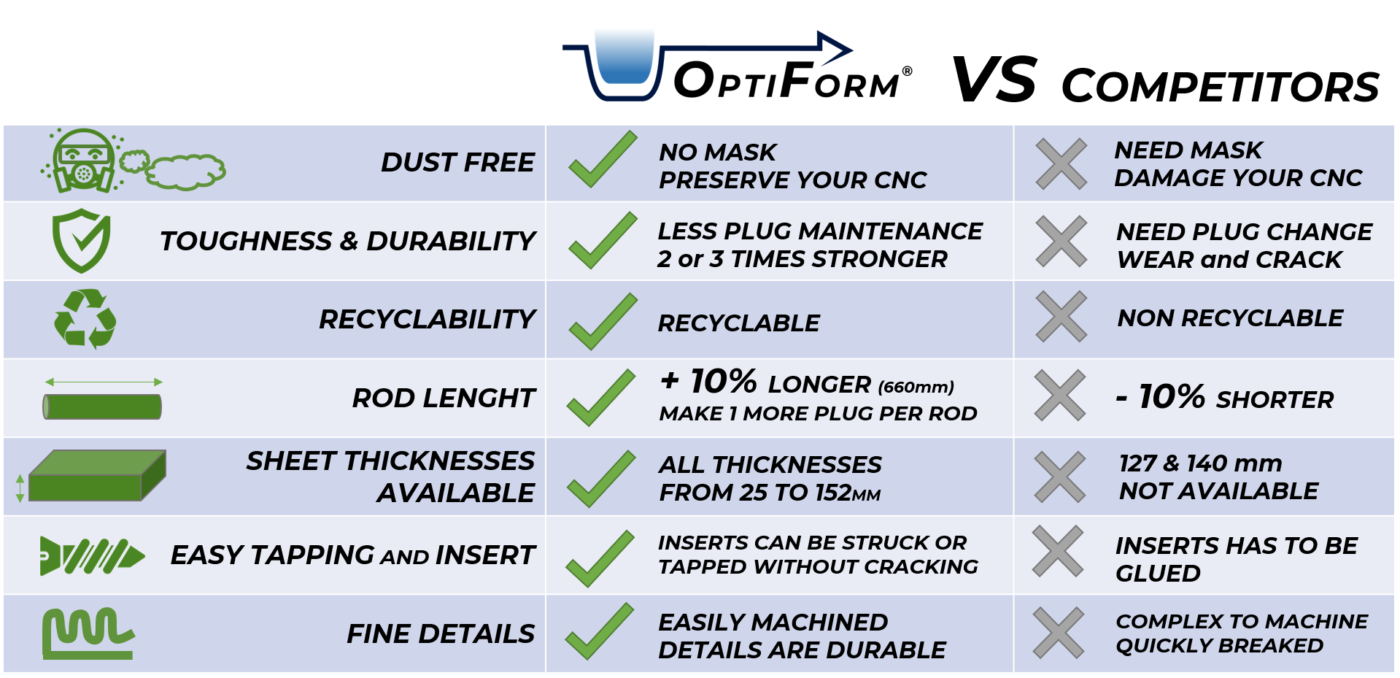
Applications
Which Thermoforming Machine
- Tilting machines
- Three-station
- Two-station
- Form Fill Seal
- Heavy-gauge Sheet fed Thermoforming machine
References of Thermoforming machine manufacturer: Illig, Kiefel, Gabler, WM machine, GN, Brown Machines, AMUT, Inpak.
Final products
Thin-gauge products
Plastic sheets that are between 0.010 inches and 0.060 inches thick.
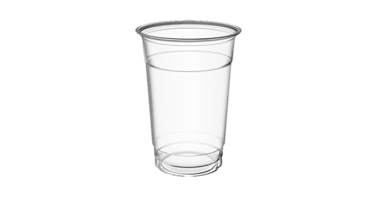
A title
Image Box text
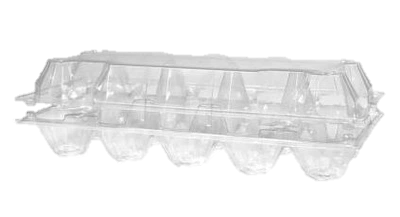
A title
Image Box text
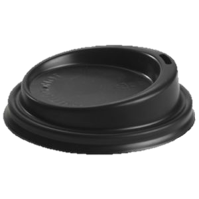
A title
Image Box text
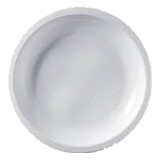
A title
Image Box text
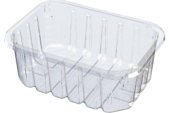
A title
Image Box text
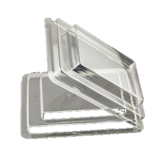
A title
Image Box text
Heavy-gauge products
Plastic sheets that are between 0.060 and 0.500 inches thick.
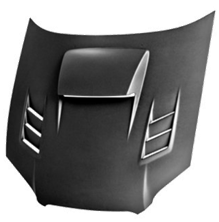
We recommend this product for optimum production :
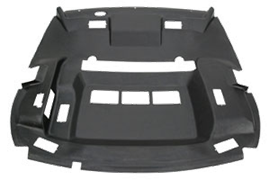
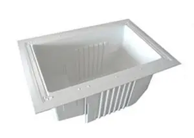
A title
Image Box text
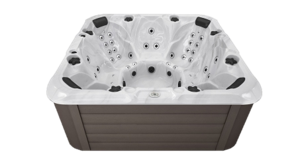
A title
Image Box text
Datasheets
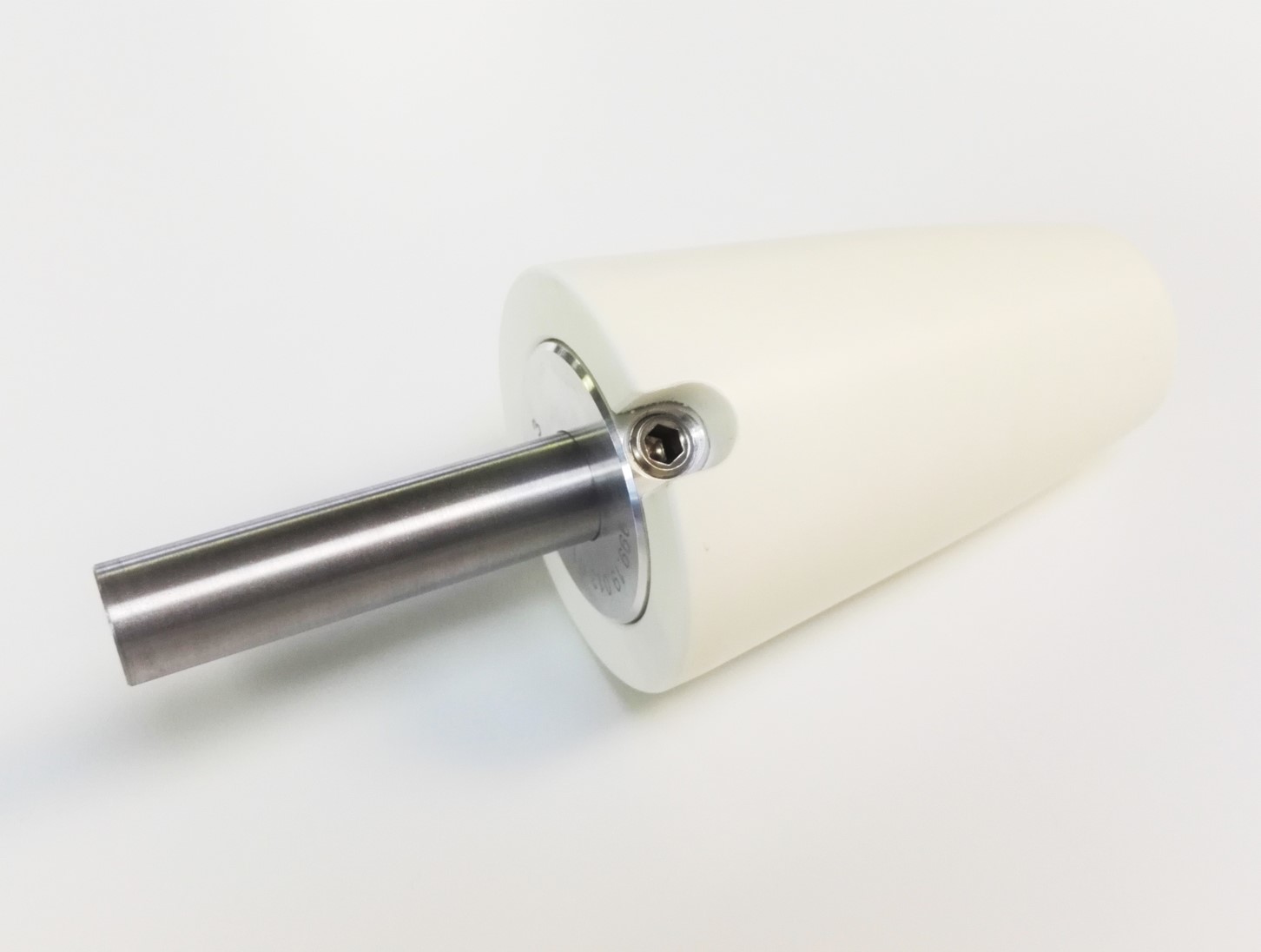
OptiForm F2X
The Standard Grade
For PS, PVC, PET
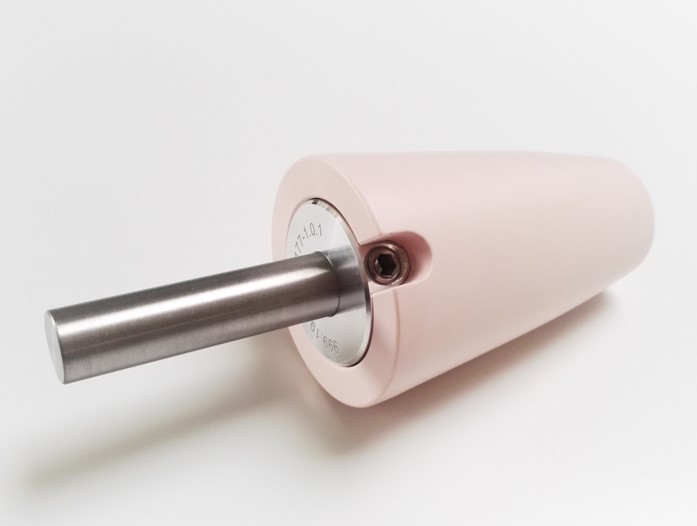
OptiForm SLX
The Smoothest
For PET, PP
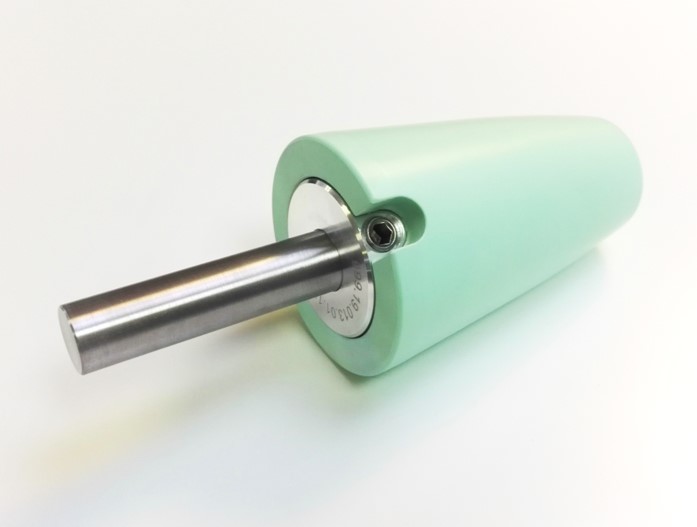
OPTIFORM FXT
The Anti Stick with Teflon
For MULTILAYER
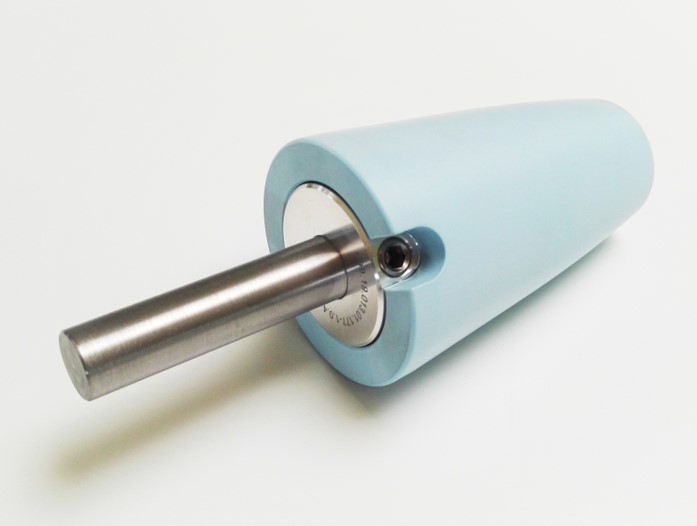
OptiForm B2X
The Most Durable
For PP, PET, PLA
Q & A
Syntactic foam is a lightweight composite material of a matrix and hollow microspheres. The microspheres, filled with gas, reduce density for weight reduction. It has high strength-to-weight ratio, impact resistance, low water absorption, thermal insulation, and soundproofing.
Syntactic foam has become the most widely used plug assist material today as a result of high performance, listed below.
Thermoforming is the process of heating a sheet of thermoplastic material and forming it to the desired shape.
The process is:
- Heat a sheet of thermoplastic material in an oven.
- Once heated to the target temperature, place the heated sheet on a mold.
- A plug assist will press the sheet into the mold. When the mold is removed, it will create a 3D object.
- Once the formed plastic cools and hardens, it is then removed from the mold and trimmed.
- The free-standing, 3D object is now ready to be painted, labeled, stamped, die cut, or enhanced in whatever way is necessary to create the final product.
Packages often require thermoforming t create custom-shaped and precise packaging solutions for various products.
Thermoforming allows:
- Customization: You can create packaging that are tailored to the exact shape, size, and dimensions of the product being packaged. This customization ensures a snug and secure fit, minimizing movenement and potential damage during transportation.
- Product protection: Thermoformed packages can provide excellent protecion for products by securely holding them in place and shieling them from external impacts, moisture, dust, and other environmental factors.
- Visibility and Presentation: Thermoforming enables the creation of transparent and clear packaging, which can be avatageous for the marketing.
- Cost-effectiveness: It is relatively cost-effective manufacturing process, especially for large-scale production. It allows efficient material usage, high production rates, and streamlined
- Versatility: It is a process that can work with various types of plastics materials, including PET, PVC, PS, and more. It allow a wide range of packaging options, accomodating different product requirements and industry needs.
Containers
why thermoforming ?
- coût d’invesitssement projet (pour débuté) surtt injecion plastique qui peut être concurrent mais plus épaisse
quels sont les possibilité des différents ouverture qu’on peut avoir?
No, thermoforming has many benefits and can be used to achieve various products packaging needs. They can be food trays, and long-lasting plastics products for various products and industries. In conclusion, thermoforming is used for thin-gauge producs and for heavy-gauge products.
They are 2 different variations of thermoforming process, which, mainly differs in the thickness of the plastic sheet used to create the finished product.
- Thin-gauge thermoforming uses plastic sheets that are between 0.010 inches and 0.060 inches thick. The process is used to create consumer goods such as, disposable cups, food packaging, clamshells, blister packs, and so on. It is a cost-effective method for producing large quantities with consistent quality.
- Heavy-gauge thermoforming uses plastic sheets that are between 0.060 and 0.500 inches thick. The process is used to create more durable products such as automotive partis, medical devices, industrial containers, and furniture components. It is optimal for the production of more complex an precise parts than thin-gauge thermoforming.
Where heavy-gauge thermoforming has a higher strength-to-weight ratio, it requires more material, more energy to heat the plastic sheet than thin-gauge thermoforming.
A wide range of plastic materials can be used in thermoforming:
- Polyethylene (PE): most commonly used in thermoforming.
- Polypropylene (PP): knonw for its high-strength and chemical resistance
- Polystyrene (PS): knonwn for its low-cost and ease of processing.
- Polyethylene terephthalate (PET) is the most common choice for a wide range of industries.
A Rigorous Quality Check
The steps we follow to give you the best products are:
- We first remove the syntactic foam from the mold.
- Then we identify the product by marking it with the part number.
- After identifying it, we machine it.
- And to finish the process we double check every products one by one by 2 operators.
- Finally, we register the quality check that has been made into a quality database.
We Remain Attentive To Your Requests Even After You Recieve Your Order!
It is important for us to accompany our clients even after they recieve their order. That’s why we ask our clients to write the part number of each products that they work with for a good traceability.
Yes we do! No matter where you are you will always have access to our products and services.
CGP tries its best to respond to your needs. And for that, we propose to you a range of products that can satisfy your expectations. We can assure that you’ll find your hapiness in our products.
All of our products are precised down bellow
F2X | SLX | FXT | B2X | ||
---|---|---|---|---|---|
MACHINABILITY Moldmaker benefits | Dust Free | ||||
Smoothness from machining | |||||
Polishing | |||||
Insert & Threading | |||||
THERMOFORMING APPLICATION Thermoformer benefits | Material distribution | ||||
Resistance to abuse | |||||
Multilayer | |||||
Deep draw | |||||
Part Clarity | |||||
Plug Durability |
F2X | SLX | FXT | B2X | ||
---|---|---|---|---|---|
MACHINABILITY Moldmaker benefits | Dust Free | ||||
Smoothness from machining | |||||
Polishing | |||||
Insert & Threading | |||||
THERMOFORMING APPLICATION Thermoformer benefits | Material distribution | ||||
Resistance to abuse | |||||
Multilayer | |||||
Deep draw | |||||
Part Clarity | |||||
Plug Durability |
We wanted to help our clients to choose the right products and right sizes as much as possible. And for that, we made a comparing table that can help you to decide on which products to order based on your needs.
In addition, we made sure that there are enough sizes for you to be satisfied. In the table of sizes, you’ll find the different sizes available for sheets and rods.
Standard Stock Sizes | Made to order | ||||||||||||||||
---|---|---|---|---|---|---|---|---|---|---|---|---|---|---|---|---|---|
Diameter or Thickness | inch | 1 | 1.5 | 2 | 2.5 | 3 | 3.5 | 4 | 4.5 | 5 | 5.5 | 6 | 7 | 8 | 9 | 10 | 12 |
mm | 25 | 38 | 51 | 64 | 76 | 89 | 102 | 114 | 127 | 140 | 152 | 178 | 203 | 228 | 254 | 305 | |
Rods (660 mm) | • | • | • | • | • | • | • | • | • | • | • | • | • | • | |||
Sheets (610 x 660mm) | • | • | • | • | • | • | • | • | • | • | • | • | • | • | • | • | |
*Other custom sizes are possible on request |
It is also possible to ask us to precut the syntactic foam in the size that you want so that you don’t have to do it and it’ll reduce your amount of scrap.
In the table down below you can find our range of available Optiform plug assist materials’ sizes.
Standard Stock Sizes | Made to order | ||||||||||||||||
---|---|---|---|---|---|---|---|---|---|---|---|---|---|---|---|---|---|
Diameter or Thickness | inch | 1 | 1.5 | 2 | 2.5 | 3 | 3.5 | 4 | 4.5 | 5 | 5.5 | 6 | 7 | 8 | 9 | 10 | 12 |
mm | 25 | 38 | 51 | 64 | 76 | 89 | 102 | 114 | 127 | 140 | 152 | 178 | 203 | 228 | 254 | 305 | |
Rods (660 mm) | • | • | • | • | • | • | • | • | • | • | • | • | • | • | |||
Sheets (610 x 660mm) | • | • | • | • | • | • | • | • | • | • | • | • | • | • | • | • | |
*Other custom sizes are possible on request |
Yes, you can! As you can see in the video below you can drill a hole and thread an insert. We guarantee the resistance and durability of our products.